The CE-hub are now recruiting for an Industrial Impact Fellow. The successful applicant will support the work of …
News
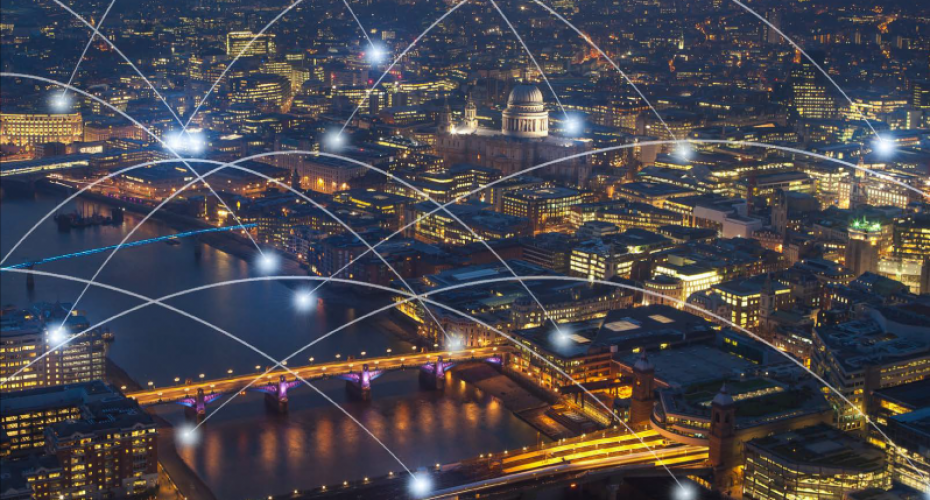
Report outlines steps needed for UK manufacturing to prepare for digital future
A major new report seeks to future-proof the UK’s manufacturing sector with five key recommendations on how best to adapt to – and make the most of – digital technologies.
The recommendations are published in the Digital World 2050 report, the result of a six-year study by the ESPRC-funded Connected Everything network, a diverse group of experts including circular economists and digital manufacturing experts, who are exploring how to support the future of UK manufacturing.
Co-authored by researchers from the Universities of Exeter, Nottingham, Liverpool and Cambridge, the report emphasises that decisions made today, and the actions of governments, industry and funders, will determine whether the potential of digital technology is maximised within the manufacturing sector.
That potential includes the creation of new jobs, data-driven business models to improve productivity, resource efficiency and business gains, as well as ways to reach net zero manufacturing, achieved in part through the creation of a digital-enabled circular economy, where materials and products have a digital footprint capturing data on product design, composition and condition that can be used to extend a product’s life.
The study draws together evidence from reports, policy literature, working papers, newsletters, government documents and white papers to understand the full range of digital manufacturing research.
Researchers also engaged with leaders from academia, industry and policy through manufacturing conferences, surveys and roundtables on four themes: industrial digital technologies in 2050; digitisation and the manufacturing workforce of the future; digital support for achieving net zero by 2050; and digitally enabled manufacturing resilience.
Across the four themes, five recommendations emerged strongly:
1. Connect digital technology developers to manufacturers
Greater support is needed to connect manufacturing businesses with the UK innovation community, creating opportunities, increasing productivity and solving industry challenges.
2. Reduce digital manufacturing knowledge barriers
Digital manufacturing solutions need to become as simple and intuitive to use as installing a new mobile phone app or using a self-service checkout. An example of this is the no-code revolution that allows anyone to create software through more intuitive visual interfaces.
3. Consolidate digital manufacturing guidance
Manufacturers seeking digital manufacturing guidance need more advice about where to start so that they can access the expertise to implement digital manufacturing solutions.
4. Support employee wellbeing during transition
Communicating clearly and consistently with employees about how the opportunities digitisation offers them can help people engage with the digital transformation and not be left behind.
5. Transparency of value chain data
Support to improve data sharing and transparency is needed to understand the environmental and social impact of manufacturing decisions and drive more sustainable choices towards a circular economy.
Other recommendations, which emerged from the roundtable discussions, included encouraging researchers to demonstrate the digital manufacturing costs vs benefits; supporting the design of sustainable products; providing financial incentives for manufacturers to decarbonise; and removing legislation preventing waste from being used as a viable alternative resource.
Co-author Fiona Charnley, Professor of Circular Innovation at the University of Exeter Business School and Co-director of the UKRI National Interdisciplinary Circular Economy Hub, said: “This horizon-scanning study will help industry identify suitable collaboration partners for future research, and determine opportunities for investment in new technologies.
“Digital technology is becoming embedded throughout manufacturing and society and has a critical and growing part to play in addressing manufacturing challenges and delivering a more sustainable, circular and resilient future. Maximising its contribution will depend on the decisions we make today, and the actions of governments, industry and funders.”
Fellow co-author Dr Oliver Fisher, formerly of the University of Nottingham and now at the University of Surrey, said: “When we started this horizon scanning work, imagining what manufacturing in 2050 would look like was a daunting prospect.
“But by bringing together of expertise from across disciplines we were able to gain new insights and perspectives on the challenges and opportunities that may emerge as digital technologies are embedded within manufacturing processes and workforces. I hope the knowledge generated within this report will help accelerate the transition towards a sustainable manufacturing future.”
Read and download the report here.
Press release by Russell Parton.